How Cleanrooms Prevent Contamination
- zachsievert15
- 5 hours ago
- 4 min read
Cleanrooms are more than just high-tech spaces—they’re essential environments where contamination control directly impacts safety, quality, and compliance. From pharmaceutical production to aerospace assembly and microelectronics, cleanrooms are designed to protect sensitive processes and products from even the tiniest pollutants. But how exactly do cleanrooms prevent contamination? Let’s explore how they work, why they matter, and what goes into creating and maintaining these controlled environments.

Table of Contents
What Is a Cleanroom?
A cleanroom is a controlled environment where airborne particles, microbes, and chemical vapors are kept within strict limits. These rooms are used in industries where a tiny contaminant can ruin an entire batch of product or lead to safety risks—think pharmaceutical labs, electronics manufacturing, or biotech facilities.
Cleanrooms are classified based on how many particles of a specific size are allowed per cubic meter of air. For example, an ISO Class 5 cleanroom allows no more than 3,520 particles (0.5 microns or larger) per cubic meter. Clean rooms can range from small bench-top enclosures to large production facilities, depending on the application and the level of control required.
The Science Behind Contamination Control
Contamination can come from just about anywhere—dust in the air, oils from human skin, fibers from clothing, or microbes from sneezing. In sensitive manufacturing environments, even these microscopic invaders can damage products or compromise results.
That’s where cleanrooms step in. By managing airflow, pressure, temperature, and humidity, cleanrooms minimize the chance that these contaminants will ever come into contact with the product or process. They also rely on proper cleanroom engineering and consistent maintenance to stay compliant.
The science of contamination control is backed by decades of research, with strict industry standards ensuring cleanrooms operate as intended. The ongoing monitoring of environmental factors is essential to uphold these standards and ensure reliability over time.
Key Features That Help Cleanrooms Prevent Contamination
Several built-in features allow cleanrooms to limit contamination effectively:
HEPA and ULPA Filters
High-Efficiency Particulate Air (HEPA) filters remove 99.97% of particles as small as 0.3 microns. Ultra-Low Penetration Air (ULPA) filters go further, capturing 99.9995% of particles down to 0.12 microns. These filters form the backbone of particle control.
Positive Air Pressure
In many cleanrooms, the air pressure is kept slightly higher than in the surrounding space. This ensures that when doors open, clean air flows outward instead of allowing potentially contaminated air inside.
Specialized Flooring and Wall Materials
Smooth, non-porous surfaces help prevent dust buildup and make the room easier to sanitize. Some materials also reduce static, which can attract and hold particles.
Controlled Environment Monitoring
Sensors are used to measure air quality, humidity, temperature, and other factors to keep the cleanroom operating within required limits.
These combined design features form a multilayered defense system that keeps contaminants away from sensitive operations.
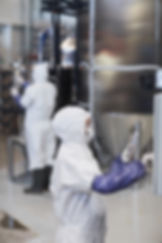
The Role of Air Filtration Systems and HVAC Design
Airflow is one of the most critical components of a cleanroom. A specialized HVAC system paired with HEPA or ULPA filters helps create unidirectional airflow that sweeps contaminants away from the workspace. This airflow is carefully engineered to avoid turbulence, which could recirculate particles back into the clean zone.
Temperature and humidity also play a role—not just for product quality, but also to ensure comfort and safety for workers. Precise climate control helps maintain consistency across cleanroom operations, which is essential for industries like biotech and microelectronics.
Designing an HVAC system for a cleanroom requires specialized knowledge of cleanroom construction, airflow modeling, and environmental load calculations. At DesignTek Consulting, we provide cleanroom HVAC solutions that are tailored to your process needs and environmental requirements.
Cleanroom Protocols and Human Behavior
Even the most technically advanced cleanroom depends on the people working inside it. Human activity is one of the leading sources of contamination, which is why strict behavioral protocols are in place.
Gowning:Â Staff must wear specialized garments like coveralls, gloves, masks, and shoe covers to minimize skin and fiber contamination.
Airlocks and Air Showers:Â Entry and exit procedures involve staged transitions and air showers that remove surface particles from garments.
Movement Control:Â Walking or moving quickly can stir up settled particles. Training teaches staff how to move efficiently and carefully.
Restricted Items:Â Only approved materials and tools can enter clean rooms to prevent contamination from outside substances.
These steps all contribute to a cleaner, more stable controlled environment. Even a well-built cleanroom can be compromised if behavioral procedures aren’t consistently followed.
Cleanroom Certification and Compliance Standards
After a cleanroom is built, it must be tested and certified to ensure it meets industry standards. This certification confirms the room is suitable for the intended process and performs as expected.
Cleanroom certification involves:
Measuring airborne particle counts
Testing airflow direction and velocity
Verifying pressure differentials between spaces
Evaluating filter integrity
Confirming temperature and humidity fall within tolerance
Most cleanrooms must meet ISO 14644-1 standards or follow Good Manufacturing Practice (GMP)Â regulations, especially in pharmaceutical and medical device manufacturing. Regular inspections and recertification help maintain compliance over time.
Construction and Design Considerations
The construction of a cleanroom involves far more than putting up walls and installing filters. From early planning through final build-out, everything must align with the cleanroom classification, product requirements, and facility infrastructure.
Important design elements include:
Layout that promotes clean-to-dirty workflow
Durable, easy-to-clean surfaces that resist corrosion and particle buildup
HVAC and air filtration systems that support environmental control
Monitoring technology for real-time feedback
Consideration for wastewater management and utility needs
A cleanroom contractor or cleanroom builder with experience in cleanroom design and construction management ensures these details are handled correctly from the start. Mistakes during the build phase can be expensive to fix later, especially if the cleanroom fails certification.

How DesignTek Consulting Supports Contamination Control
At DesignTek Consulting, we specialize in designing and engineering cleanrooms that meet your performance and compliance goals. From early-stage layout planning to HVAC system integration and cleanroom certification readiness, our team delivers services for industries that demand precision and cleanliness.
We understand that contamination control starts long before the room is operational—it begins with thoughtful design, smart construction, and reliable systems that work in harmony. Ready to take the next step in building or upgrading your cleanroom? Contact us to learn how we can help with cleanroom construction, HVAC system planning, and project management built around your needs.