Cleanrooms in Electronics Manufacturing
- zachsievert15
- Aug 13, 2024
- 3 min read
Updated: Nov 15, 2024
Electronics manufacturing demands extreme precision and cleanliness. Even a tiny speck of dust can ruin an entire batch of products, leading to costly delays and rework. Cleanrooms are essential in preventing such issues. These controlled environments ensure that electronics are manufactured under the cleanest conditions possible, protecting sensitive components from contaminants. Understanding the importance of cleanrooms in this industry is crucial for maintaining high standards of quality and efficiency.
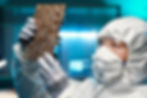
What is a Cleanroom?
A cleanroom is a controlled environment where pollutants like dust, airborne microbes, and chemical vapors are minimized. These rooms are designed to maintain extremely low levels of particulates, achieved through a combination of specialized HVAC systems, air filtration systems, and rigorous operational protocols. In electronics manufacturing, cleanrooms ensure that sensitive components such as semiconductors, microchips, and circuit boards are produced without contamination, ensuring high quality and reliability.
The Role of Cleanrooms in Electronics Manufacturing
Protecting Sensitive Components
Electronics manufacturing often involves working with tiny components, some smaller than a grain of sand. A cleanroom prevents these components from being contaminated, which is crucial because even the smallest particles can cause defects or failures in electronic devices. For example, a single particle can cause a short circuit in a microchip, rendering it useless.
Enhancing Product Quality and Yield
Maintaining a cleanroom environment is directly linked to product quality. By reducing contamination, cleanrooms help ensure that products meet strict quality standards. This, in turn, increases yield, as fewer products are rejected due to contamination. For companies, this means higher efficiency and profitability.
Meeting Industry Standards
In the electronics industry, compliance with industry standards is non-negotiable. Cleanrooms are often required to meet specific standards, such as ISO 14644, which defines the cleanliness levels in various industries. Meeting these standards is not only important for product quality but also for regulatory compliance.
Designing and Building Cleanrooms for Electronics Manufacturing
Cleanroom Design and Engineering
Designing a cleanroom for electronics manufacturing requires specialized knowledge and expertise. The layout, air filtration systems, HVAC systems, and materials used must all be carefully selected to meet the specific needs of the electronics being produced. At DesignTek Consulting, we specialize in cleanroom design and cleanroom engineering tailored to the unique requirements of your manufacturing process.
HVAC Systems and Air Filtration
The HVAC system is the backbone of any cleanroom. It controls the temperature, humidity, and airflow, ensuring that the environment remains stable and contaminant-free. Air filtration systems are equally important, as they remove particulates from the air before it enters the cleanroom. High-Efficiency Particulate Air (HEPA) filters are commonly used in cleanrooms to achieve the desired level of air cleanliness.
Construction and Installation
Building a cleanroom is a complex process that requires careful planning and execution. A cleanroom contractor with experience in the electronics industry is essential to ensure that the cleanroom is constructed to meet industry standards. At DesignTek Consulting, we offer comprehensive cleanroom construction services, including construction management and wastewater management solutions to ensure your cleanroom is fully operational and compliant with all regulations.

Maintaining and Operating Cleanrooms
Regular Cleaning and Maintenance
Once a cleanroom is operational, maintaining its cleanliness is a continuous process. Regular cleaning and maintenance are crucial to prevent contamination. This includes cleaning surfaces, changing filters, and monitoring environmental conditions. Staff working in cleanrooms must also follow strict protocols, such as wearing protective clothing and minimizing movement to reduce the risk of contamination.
Monitoring and Validation
Continuous monitoring of the cleanroom environment is essential to ensure it remains within the required specifications. This includes monitoring air quality, temperature, and humidity levels. Validation is also important, where the cleanroom is tested to ensure it meets the required standards. This process is usually done regularly to maintain the cleanroom’s integrity.
Upgrades and Renovations
As technology advances, the requirements for cleanrooms in electronics manufacturing may change. Upgrading or renovating your cleanroom may be necessary to meet new standards or accommodate new manufacturing processes. Working with a knowledgeable cleanroom contractor can help you navigate these changes seamlessly.
Partnering with DesignTek Consulting for Your Cleanroom Needs
Cleanrooms are an indispensable part of the electronics manufacturing process. They protect sensitive components from contamination, ensure high product quality, and help meet industry standards. Whether you're designing a new cleanroom or maintaining an existing one, it's important to work with experts who understand the specific needs of the electronics industry.Â
At DesignTek Consulting, we offer a full range of services, from cleanroom design and cleanroom engineering to cleanroom construction and maintenance. Contact us today to learn how we can help you create a cleanroom that meets your manufacturing needs.